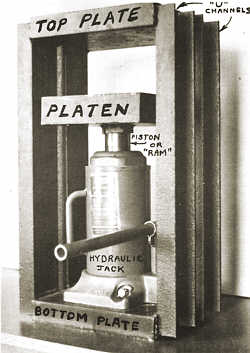
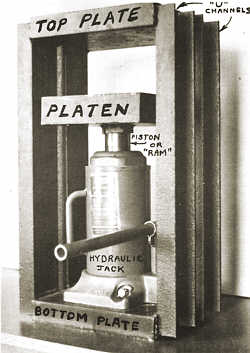
The Practical Hydraulic Press
How do you solve the problem of producing a limited edition of hand wrought, hollow forms in a reasonable amount of time, and yet have them fit together and look fairly identical without looking machine made? Raising, chasing or masonite die-forming might be an answer, If you are fast and accurate enough at it. But even then, those methods can't compare with the speed, ease and precision offered by the inexpensive, simple, practical forming of such pieces by use of dies and a small hydraulic press.
16 Minute Read
How do you solve the problem of producing a limited edition of hand wrought, hollow forms in a reasonable amount of time, and yet have them fit together and look fairly identical without looking machine made? Raising, chasing or masonite die-forming might be an answer, If you are fast and accurate enough at it.
But even then, those methods can't compare with the speed, ease and precision offered by the inexpensive, simple, practical forming of such pieces by use of dies and a small hydraulic press.
Marc Paisin, Soap Bubble Blower |
The equipment used is simple to build and the processes are easy to master. Using this process, you can quickly form sheet metal into hollow forms that fit together for soldering with a minimum of work and almost no finishing or loss of metal, thereby allowing the use of a thinner gauge metal. Hang in there and we'll cover how to do it all, but for a moment take a look at how it all developed.
Development
Die-forming of sheet metal originally began thousands of years ago, by utilizing crude grooves carved into stone or wood, into which the metal was freely manipulated by hand and hammered into the depression. Dies were used for handles, spouts and forms that couldn't be made on stakes.
Within the last 150 years, however, die-forming concepts have undergone a tremendous technological evolution. Most important was the creation of mate-female conforming dies to create hollow forms utilizing hydraulic pressure or drop hammer presses. (The terms "male" and "female" conforming dies are standard industrial jargon for dies which conform in shape… the symbolism is obvious.)
Today, hydraulic pressing and stamping of dies are used very extensively throughout industry to form everything from pots and pans to automobile bodies. Nonetheless, very few individual artist-metalsmiths have utilized this technique on a small, inexpensive scale to produce forms in silver or gold.
To adapt hydraulic pressing equipment and techniques to a small, inexpensive scale, experiments were conducted using an adapted version of the original masonite die technique which was developed by Richard Thomas of Cranbrook Academy of Art. A small, war surplus, embossing Press was originally used. This research was initiated by Ruth Girard at the University of California at Berkeley , in 1971 and led to eventual development of pourable epoxy-steel molds on a small wale. I have continued the research since that time, and wish to share the results with you, now.
The Process
Hydraulic pressing of conforming dies starts with a 3-dimensional model or pattern which is used to mold male and female dies which conform in shape, to the model and each other. The dies are then inserted in the press and sheet metal is placed between the dies. Then hydraulic pressure is applied, in order to press the metal into the desired form. Industrially, most dies am made of steel or pourable epoxy-metal material and the presses are commercially purchased and can generate a pressure up to 3,000,000 lbs. per square inch' Needless to say, equipment and dies like that could cost a mint.
Therefore, adpating the processes for our use, involved making an inexpensive press as well as dies. Utilizing the adapted techniques, you can press gold, silver, copper or brass sheet metal ranging from 24 Ga. to 16 Ga., with little trouble. 24 Ga. is the upper limit, since metal any thinner tends to tear, krinkle, crimp or fold in pressing in these molds. Metal thicker than 16 Ga. creates a need for extreme hydraulic pressure as well as a more sophisticated mold, made of steel. Nonetheless, this range of gauges seems to encompass most of the hollow forms work done by artist-metalsmiths.
Sooooo, let's take a look at how to make a press and dies.
The Press
It you have the money, you can purchase a fine, commercial, hydraulic press for about $1 000 or you can make a suitable am of your own for under $50 and some elbow grease. Essentially, all the press consists of is a strong steel frame into which a hydraulic ram is inserted and used to press one of the dies against the other.
Illustration 1 - welded press frame and hydraulic jack. |
The Steel Frame
To make a welded frame, first scrounge around for your cheapest source of scrap or junk steel, and locate pieces of "U" channel or "IL". (They are called "U" or "L" because the piece of steel looks like a "U" or "L" when viewed from the end. Select metal that has a wall thickness of 1/4 inch or greater (the bigger the better). You'll need enough for four side pieces, the length of which depends on the height of the hydraulic jack or ram you get, but usually, 6 or 7 feet all total, is enough.
You'll also need 3 pieces of sheet metal, 3/8″ thick or greater, to same as the top, bottom and platen. Here again, find your cheapest source, as the meta I need not be new, only flat.
Lastly, you'll need a piece of pipe to weld an the underside of the platen, so the hydraulic ram can fit to the platen. The diameter of the pipe will depend on what diameter man you come up with. The pipe should be just a little bigger than the man.
Now, cut and arrange the pieces as in the illustration (1), then weld away … and you've got a press frame. What's that? You say you've no welding equipment? Fear not, as you can make a bolt together model, that's almost as strong.
The bolt together frame can be made from hardware store items plus the three pieces of sheet steel for the top, bottom and platen. Most hardware stores carry threaded stock in 2 or 3 foot lengths, and in various diameters. Also, they usually carry washers, nuts, and pipe. That's all you'll need in order to substitute for the "U" or "L" steel. Purchase 4 pieces of threaded stock of 1/2 inch or greater, diameter, each about 2 feet in length, Also, get 16 flat washers for that diameter stock as well as 16 nuts. Then, you also need 4 pieces of pipe big enough to slide the threaded stock into. Their length depends on the height of the hydraulic jack or ram you end up with (see illustration 2). Lastly, you'll still need the little piece of pipe to fasten to the underside of the platen, as in the welded model.
To assemble these parts, start by drilling four holes in the top and bottom pieces of sheet steel. The holes should be just big enough for the threaded stock to slip through. Cut the pieces of pipe to a length equal to the height of the hydraulic ram in its fully extended position, with the platen sitting on top of it. Now, thread two washers and 2 nuts onto one end of each of the four pieces of threaded stock. Then, place the bottom plate on the threaded stock, using the four holes. You can then stand the whole gizmo upright, and place a piece of pipe over each of the four threaded pieces, followed by the top plate. Again, thread two washers and 2 nuts onto each of the threaded stock pieces, tighten them up with a wrench, and you have a bolt together hydraulic press frame.
Illustration 2 - bolt together frame. |
The Hydraulic Ram
Flea markets and junk shops are great sources for used hydraulic jacks for cars and trucks. So, scrounge around for a 20 ton capacity, hydraulic truck jack, (a 15 ton jack will make do, but a 20 ton is preferred, as you won't have to Pump as hard.) You most probably can get one for $20 or less, since they are only about $50 new. They are complete and ready to go, as long as you get one in good condition. About the only things that wears out, are the "0" ring seals. Virtually all manufacturers sell a self-explanatory seals replacement kit for their jacks, for about $5, if you should run into that problem.
Just place the lack in the frame, center the platen on the head of the jack, and mark its location on the underside of the platen. Then weld the small piece of pipe on the underside, to locate the ram head on the platen. If you've no welding equipment, roughen and clean both surfaces and use some Devcon Plastic Steel (putty type) to fasten it. Now, you're ready to fly or should I say squash.
As an alternative to a truck jack, you can scrounge around for a used industrial hydraulic ram of 2″ or greater diameter, at used industrial supply outfits or hydraulics dealers. The larger the ram diameter, the less pumping force you need, in that the pressure at the platen is equal to the pumping pressure times [p * R 2] , where R is the radius of the ram head So, bigger rams mean less effort. If you do locate an industrial ram, it most probably will have a fitting on it for a pressure gauge. If so, get a cheap used one, and you can then determine just what pressure you are pressing at. Most of the pieces I've done have been pressed at 26,000 lbs/sq. in. or less.
Marc Paisin Devcon die and flask |
Dies
Many dies are suitable for hydraulic In pressing, ranging from the use of a conventional masonite die with the addition of a male die, to the use of cast male and female conforming dies of metal, pourable epoxy-steel or fiberglass. Which do you use when? In general, the greater the detail and the tighter the curves, the more the need for the dies to be made of hard material such as metal or epoxy-steel and to have male-female conformity, especially it ten units or more are to be produced.
Use the adapted masonite die only when you have gradually sloping curves of large radius, and not too much detail. This is because you have a male die and an outline of the female die, but no female conformity. This inexpensive die is made from a sheet of tempered masonite fastened to '3/4 inch pieces of plywood, with the outline of the piece cut out of the masonite and plywood. For pressing, it is adapted by adding a male die and locating pegs made from large nails. The male die can be sculpted from hardwood such as oak or maple or it can be cut and filed from a thick piece of aluminum or cast in brass, bronze, aluminum or the like. To prevent deterioration of the forming edge of the masonite, a 16 Ga. piece of sheet steel can be cut with a jeweler's saw to produce a template outline, if you wish to produce many units.
Far and away, the best dies are the cast male-female conforming dies. They have the distinct advantages of being made of harder materials (therefore allowing more units to be produced with better detail and slower deterioration of the dies) as well as providing full forming with male-female conformity. Additionally, they too are relatively inexpensive.
I recommend use of pourable epoxy-steel as a die material, as it is quick and easy to make. Start out by sculpting the model or pattern in just about any material ranging from plasteline clay to wax, plaster, wood, plastic, metal, etc. Be sure there are no undercuts in the form. Then if this material can take about 160 degrees F. or so, you can follow the steps below, to pour the cast die. If, however, it is made of plasteline clay, wax, or some other substance that can't lake the heat, then simply coat it with a release agent such as silicone spray or light oil or even vaseline, and pour a plaster mold which you can use to pour the case die. (Plaster or wood dies should be given a coat of lacquer before proceeding, since this will seal their porous surface and allow the model to release easier.)
The epoxy-steel, or "plastic steel" used, is made by Devcon Corporation, of Danvers, Mass. Devcon produces a fine line of plastic steel products for making tools, jigs, fixtures, metal forming dies, models, molds, foundry patterns and for repairing machinery. I recommend use of their Plastic Steel B , liquid type, (Stock No. 10210). It comes in 1, 4 and 25 lb. cans, and costs about $5/lb. in one pound cans. It is available at most large hardware stores and from tooling Supply houses. It is made from 80% steel powder and 20% epoxy resin binders. The "B" liquid type is used for pouring the dies, since it is very liquidy when mixed for use. It has a compression strength of 18,000 P.S.I. with ultimate tensile strength of 10,000 P.S.I. and a Rockwell hardness rating of 93. It can be sawed, filed, tapped, drilled, ground and threaded and generally worked with metal working tools.
Now, let's proceed in making the dies. First, take your model or pattern or Plaster mold and put it in a small, strong container of some sort. (I usually use a short section of old pipe or a metal flask from the centrifugal casting rig.) Then, lubricate the pattern as well as the inside walls of the container with the release agent provided in the Devcon kit. Now, just follow the included instruction sheet in the kit, and mix up the plastic steel material. Pour it into your mold, being sure the surface you are using is not on an angle, so that the top and bottom surfaces of the plastic steel die will and up being parallel.
The Devcon material will harden at room temperature and be ready for use in about four hours. Assuming you've made no undercuts on your model and that you put enough release agent on it, your die should separate from the model and container with little trouble. If you started from a male form, you now have a female die, whereas if you started from the plaster mold, you'll have a male die. In either case, you can now repeat the same procedure and pour the other die by lubricating the surface of the Devcon die and the walls of the container and pour in more Devcon. If you plan to press 18 Ga. or thicker metal, you'll have to allow some room for the metal in the die, before pressing. Since Devcon can be filed, sanded, etc., simply take down the edge of the male die to allow for the thickness of the metal, before proceeding to pressing.
Cast metal conforming dies can also be used quite successfully for pressing, utilizing ordinary foundry techniques, if you have access to one. I'm purposely not describing how to do that, since we are talking about a regular lost wax casting or sand casting in bronze, aluminum or the like.
However, if you've been able to make your model from a piece of aluminum or the like, or if you have made a plaster mold from your original pattern, you can pour a simple, inexpensive, highly usable mold from zinc, without the use of a foundry. Find a junk source of zinc printer's plates and simply melt them down and pour directly over the aluminum or plaster, in a container. Since zinc melts at below 800 degrees F, it can be melted in a can, with a torch and cast without any further hubbub. If you have the aluminum male model, it can be used directly in the press along with the zinc female. (They will mate, even though different species.) If, however, you poured the zinc into the plaster, you can use the cooled zinc die to pour the other zinc into.
Marc Paisin, Milk Bone Box |
Pressing the Form
To press a form, just follow these steps:
- Cut a piece of the desired sheet metal, big enough to cover the cavity in the female die plus about 3/8 inch extra all around the outline of the form to be pressed. This allows for metal to be drawn down into the female die. The bigger the extra flange, the better. This metal can be cut off later and re-used for casting, etc.
- Anneal the metal.
- Place the female die in the press, inside the pipe, flask or other strong container used to cast the die in. (This metal band or container will usually prevent the Devcon die from shattering or cracking if over-pressed.
- Coat the surfaces of the dies with a lubricant of thin oil or silicone spray to aid the metal in easing into the female die and to avoid deforming the edges of the die.
- Place the sheet metal on top of the female die, and center the male die on top of the female die.
- With this assembly in the press, begin pressing by hand pumping the hydraulic ram.As you start pressing, watch for signs of crimping, folding or krinkling in the metal. When or if these appear, stop pressing and remove the sheet metal from the die.
- Use a leather mallet and anvil to smooth out the crimps and return the sheet metal for continued pressing. Repeat this process as necessary. If you've had to remove it 3 or 4 times, I suggest that you again anneal the metal.
Most forms will pick up the complete detail in the pressing. However, additional detail can be rendered in a jiffy, simply by planishing or tooling the metal, right on the male die, since the Devcon can safely take the hammering.
If you intend to produce many units in the die, you may want to cut an outline of the form in 18 or 16 Ga. steel, which can be set on the female die, thereby slowing down the deterioration of the forming edge of that die.
Other Uses for The Press
Found Objects as Dies
Try using found objects of any hard metal or cut metal to shape and press into a piece of annealed sheet metal backed up by a sheet of lead or hard rubber. You'll find that the images are quite distinct and can be very dynamic. depending on your design.
Pressed Photo Images
You can also use the press to create photo images pressed into the metal. To accomplish this, simply select a photo image or line drawing, etc., which has fairly high contrast. Then get a magnesium or zinc printer's plate made from the art work, at a photo engraving shop. Such shops are common and the cost should be about $10 or so, for a small plate. However, you can probably get quite a few images on one plate
Then, place the annealed sheet metal on top of the etched plate, topped by a sheet of lead or hard rubber, and press away. You'll find you can obtain a fairly crisp image transferred to the metal.
Conclusion
I'm sure there are some important details I've forgotten to mention and that there are other details I've purposely left out so as not to complicate this presentation needlessly. However, it is my hope that the information contained here is clear enough that you can get started, inexpensively, in hydraulic pressing. Since the adaptation of this technique is fairly new,
S.S Tea - Tea Caddy |
I encourage you to experiment and find newer and better methods and equipment for pressing, as I'm convinced its application opens up a whole new exciting technique for our use.
So remember - "if it'll stand still … PRESS IT!"
You assume all responsibility and risk for the use of the safety resources available on or through this web page. The International Gem Society LLC does not assume any liability for the materials, information and opinions provided on, or available through, this web page. No advice or information provided by this website shall create any warranty. Reliance on such advice, information or the content of this web page is solely at your own risk, including without limitation any safety guidelines, resources or precautions, or any other information related to safety that may be available on or through this web page. The International Gem Society LLC disclaims any liability for injury, death or damages resulting from the use thereof.
Related Articles
Low-Cost Press Forming Technique
The Rush Job From Hell
Live And Let Die (Struck)
Cold Forging of Karat Gold Findings
The All-In-One Jewelry Making Solution At Your Fingertips
When you join the Ganoksin community, you get the tools you need to take your work to the next level.
Trusted Jewelry Making Information & Techniques
Sign up to receive the latest articles, techniques, and inspirations with our free newsletter.