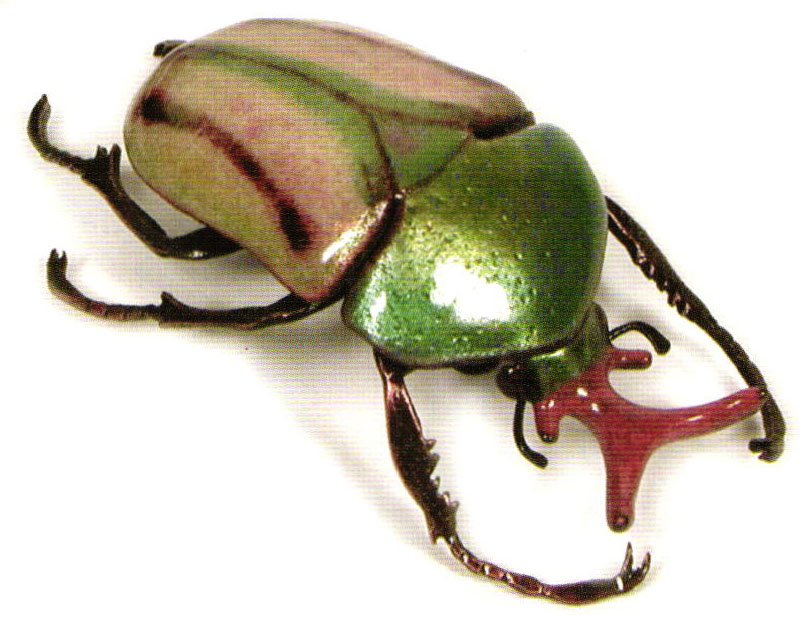
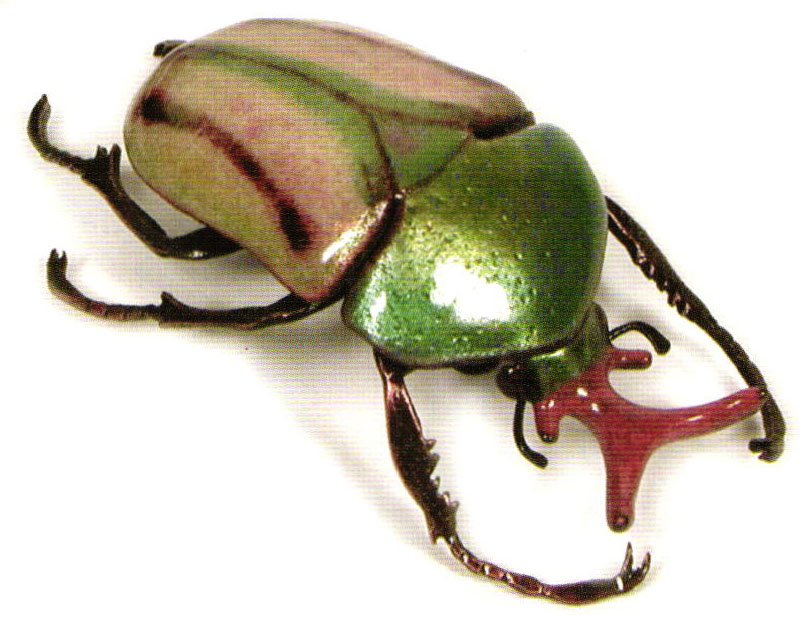
Collaborating with Insects
9 Minute Read
It took a certain level of obsession for us to combine our efforts and build a body of work around insects. We both could see how beetles, with their incredible jewellike coloring, amazing patterns and mechanical looking bodies, would make great subjects for metal and enamel.
We have been frequent collaborative artists for over twenty years with common interests in natural history, photography and gardening. Some of our favorite times are spent exploring all manner of swamps, ponds and forests for treasures that make life worth living. When we're out hiking we tend to scan the ground for interesting details and have to remind ourselves to look up and enjoy the scenery. It's not unusual for us to spend the better part of an hour trying to photograph an iridescent green tiger beetle, while hikers pass by giving us quizzical looks. We tend to make observations and gather ideas in a similar way and this helps us to come to some harmonious conclusions when we work together.
The purpose of much of our work with insects is not necessarily to strive for an impossible realism, but to enhance aspects that capture the feeling or perhaps even the 'personality' of each one. Occasionally we encounter people who have an innate fear of insects or 'creepy-crawlies'. It's interesting to see them trying to balance their appreciation for the beauty of the enamels and their primal uneasiness with the subject. We probably shouldn't have been surprised by this, but it hadn't occurred to us that some people might be afraid of our sculptures! On the other hand, it is wonderful to see how fascinated people can be when given a view of an insect as a beautiful object unto itself. Our insect sculptures have found their way into galleries, exhibitions at museums and botanical gardens and have prompted commissioned work.
Research material for our work comes from a variety of sources. Photographs, visits to museum collections, specimens furnished to us for commissioned work, and lots of internet searches yielded the views we needed to be confident that we could do some justice to the amazing design that insects possess. A helpful and encouraging interest in our efforts came from our first buyer Brett Ratcliffe, curator of insects and professor at the University of Nebraska State Museum and one of the world's foremost experts on scarab beetles. We had to assure him that our scarab sculptures had the correct number of tarsal leg segments before he would commit to a purchase! Needless to say, his endorsement was a real boost to our enthusiasm and confidence in the project. This also had the effect of moving us towards achieving more realism than we had originally planned.
There is an almost infinite amount of miniscule detail in the average beetle and the first things we consider are the qualities that can and need to be transferred to our work to get the essence of the creature across. Insects have exoskeletons. These have the appearance of interlocking plates and it is our interest in those parts taken individually that led us to a sense of how they work and fit together as a whole. We choose to focus on the three most visible upper body parts, the head, pronatum (middle) and elytra (wing covers). Our intent is to mix enameled and metal sections into one sculpture.
To do this, a parts list is developed that enables us to build and pre-fit subassemblies. These need to be removed for enameling and reattached for final assembly. Once we determine our parts list, Diane develops patterns representing each section as a flat drawing. At first she had to make some guesses about how to represent a three - dimensional object as a flat shape. Also, some allowance had to be made for the stretching and distortion of the metal during raising. She chose to work with two different gauges of flat copper sheet as it was immediately evident that the legs would need to be made from heavier stock than the upper body parts. After a number of experiments (and a scrap pile of failed thoraxes, mandibles and rhinoceros beetle horns), she developed a good sense for proportionally adjusting her patterns. The final pattern is transferred to a copper sheet and sawed out. The parts are textured and detailed while they are still flat using a variety of punches, grinders and chasing tools. Such texturing makes for work-hardened parts that need to be annealed with a torch prior to forming and raising. As in any raising process, it is necessary to anneal the parts a few times as they are being shaped. Diane has found Delrin™ sand-filled dead-blow hammers to be helpful in preventing arm and wrist injuries by absorbing the shock of repetitive hammering. A variety of spoon shaped stakes have been the most useful for raising the final forms. The legs are cut from the heavier sheet and ground into a more refined shape with a hand held rotary grinder and textured.
When Diane makes the head, pronatum and elytra subassembly, overlapping extensions are incorporated into the design that allows for brazing the three sections together. A post is brazed to the underside to enable final attachment to the lower body and legs. Be-cause this three part assembly will usually be enameled as one piece, special attention has to be given to achieving a thin, even braze at the overlapping joints. An excessive build-up of the brazing alloy may cause cracking on the overlaying enamels. The melting point of the silicon bronze brazing alloy exceeds the temperatures needed for enameling so these assemblies survive multiple firings without a problem. The three piece top is set aside while the underside and leg assembly is completed. This will be fitted to the top before preparations are made for enameling.
Sharron will use copies of Diane's pattern drawings to develop value and watercolor sketches while working up a list of enamel possibilities. Over the years she has developed techniques to combine leaded and unleaded enamels in her work. This enables her to utilize the best characteristics of each and allows for far more color choices. Every enamel and combination that she uses for the piece will be tested for color relationships as well as expansion and compatibility. Enamels from three different manufacturers might be used on a given piece, including Cristallerie de Saint-Paul (leaded and unleaded), Thompson (unleaded and leaded), and Schauer.
Before enameling, oxidation from brazing is first removed using soft abrasive wheels and then the piece is submerged in a warm Sparex™ solution for a final cleaning. Sharron will use Scalex™ on parts of the assembly that are to remain free of enamel. These might be very delicate parts like antennae, or any textured metal surfaces we might choose to use alongside the enamel in the design. The first application of enamel is a base color sifted on the top surface with counter enamel applied to the underside. After this initial base coat is fired, the piece is stoned to roughen the surface and allow for better adhesion of the next layer. Subsequent enameled layers are wet-packed with unwashed 150 mesh enamel. It is important to control the amount of distilled water used when wet-packing a curved surface like a beetle body. If the enamel is too wet it will tend to slide and end up as a soggy blob on the workbench. Thin wet-packed layers are repeated until the desired color and pattern is achieved, then followed with a final stoning and firing.
The enameled subassembly will be attached with low temperature solder to the lower body and legs using the mounting post. A final oxidized finish is given to the copper parts to bring out the texture. The beetle is now complete. If we choose to incorporate it into a larger sculpture we will collaborate again on the final design.
Recently we have been developing ideas that place our insects into enlarged fragments of magnified worlds, utilizing steel, copper and other metals to represent vegetation, man-made objects and mechanical parts. Our latest sculptures with grasses have been influenced by our volunteer work in the Herbarium of the Yale Peabody Museum, where we have been mounting grass specimens collected in the early years of the twentieth century. More views of our work can be seen at www.beetlesculpture.com.
The enameled insects have been and will continue to be something we enjoy doing but lately we have contemplated some new directions. Sharron's recent move into an interesting 1960's contemporary home with lots of available wall space has inspired us to think about designing large spreading wall sculptures and architectural murals. We look forward to the challenge of developing and constructing large scale enamels and metalwork.
Each of us maintains our own workshop. Diane has converted the lower level of her house into two workshops. One is devoted to metalsmithing and the other is a combination welding area and machine shop. She was fortunate to acquire a large collection of old silversmithing tools including stakes, anvils, and hammers of an amazing variety, all of which have come in very handy for shaping our insect bodies. Sharron and her husband have recently purchased a house where she is converting what was once an orchid growing room into an enameling studio. The room offers excellent natural light and accommodates two kilns, a drawing table and workbenches for enameling and metalsmithing.
About the Authors
Sharron Kree holds a BFA in enameling and silversmithing from the Cleveland Institute of Art. She has been employed as a designer for a commercial enameling company for over twenty years. This involves not only designing products but also developing production tooling, enameling methods, training and troubleshooting. She also serves as technical advisor in the use of Cristallerie de Saint-Paul enamels for customers of the US distributor. When she is not thinking about enameling, she spends most of her time being a caretaker of the wildlife sanctuary that surrounds her home.
Diane Buettner is a self-taught metalsmith, welder and sculptor. She has worked in the commercial craft field for over twenty years. Currently she is employed as a product development director and designer for a commercial enameling company. In addition to the creative side of this work, she designs and develops production line systems. Her other interests include guitar playing and listening to jazz, early country and blues music.
More images of Sharron and Diane's creations can be found at www.beetlesculpture.
All photographs Copyright © Buettner Kree LLC.
You assume all responsibility and risk for the use of the safety resources available on or through this web page. The International Gem Society LLC does not assume any liability for the materials, information and opinions provided on, or available through, this web page. No advice or information provided by this website shall create any warranty. Reliance on such advice, information or the content of this web page is solely at your own risk, including without limitation any safety guidelines, resources or precautions, or any other information related to safety that may be available on or through this web page. The International Gem Society LLC disclaims any liability for injury, death or damages resulting from the use thereof.
Related Articles
Jewellery in Transition
Lori Talcott: As Large as Life
Setting a Three Stone Ring with Foredom Tools
The Mysterious Power of Gold
The All-In-One Jewelry Making Solution At Your Fingertips
When you join the Ganoksin community, you get the tools you need to take your work to the next level.
Trusted Jewelry Making Information & Techniques
Sign up to receive the latest articles, techniques, and inspirations with our free newsletter.