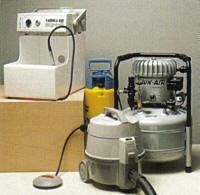
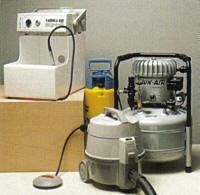
Fine Matte on Metal Surfaces
A micro-waterjet device can be used to achieve fine matt finishes on precious metal surfaces. Parts required for this are: jet or wet lap hammer, slow-running compressor, vacuum apparatus, and pressure sprayer.
2 Minute Read
A micro-waterjet device can be used to achieve fine matte finishes on precious metal surfaces. Parts required for this are: jet or wet lap hammer, slow-running compressor, vacuum apparatus, and pressure sprayer.
You assume all responsibility and risk for the use of the safety resources available on or through this web page. The International Gem Society LLC does not assume any liability for the materials, information and opinions provided on, or available through, this web page. No advice or information provided by this website shall create any warranty. Reliance on such advice, information or the content of this web page is solely at your own risk, including without limitation any safety guidelines, resources or precautions, or any other information related to safety that may be available on or through this web page. The International Gem Society LLC disclaims any liability for injury, death or damages resulting from the use thereof.
Related Articles
Platinum Finishing 2 – Procedures and Supplies
Inlay Work
The Basic Techniques of Shell Inlay
Tips & Techniques for Popular Finishing Touches
The All-In-One Jewelry Making Solution At Your Fingertips
When you join the Ganoksin community, you get the tools you need to take your work to the next level.
Trusted Jewelry Making Information & Techniques
Sign up to receive the latest articles, techniques, and inspirations with our free newsletter.