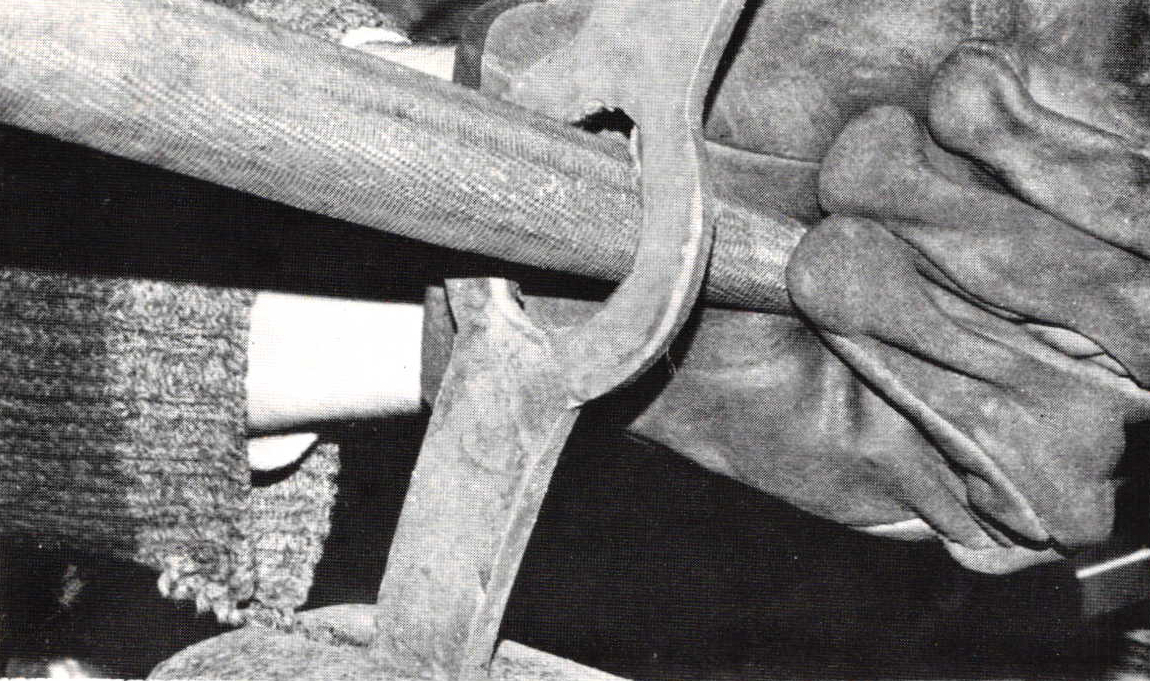
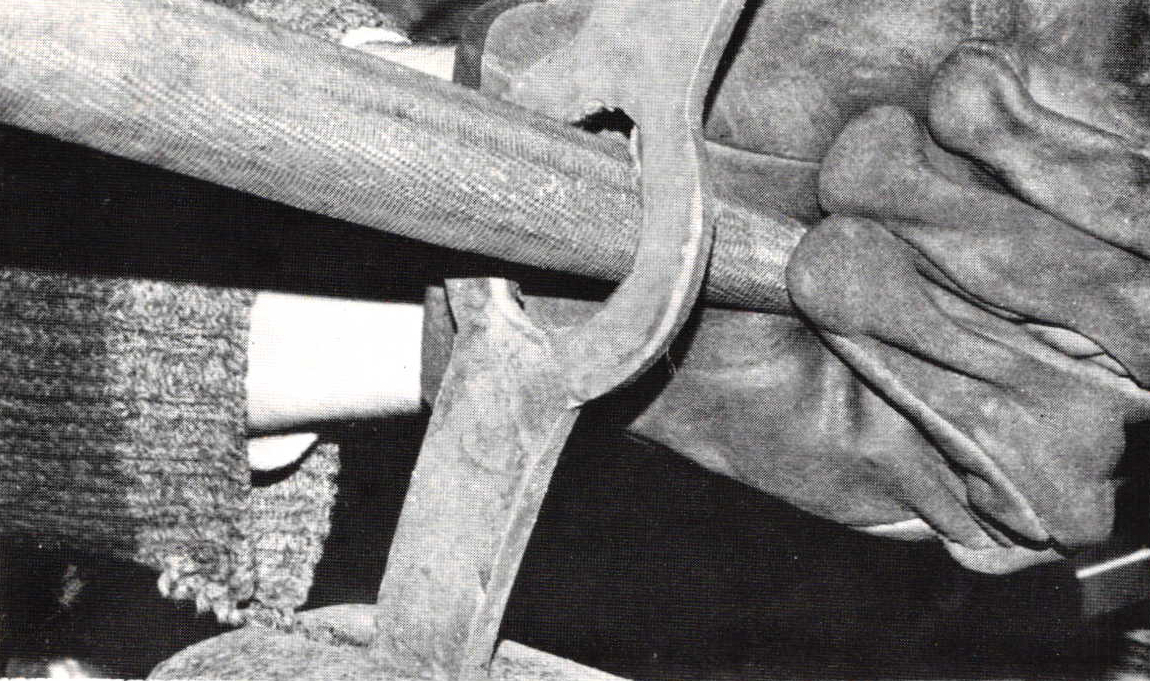
Application of Hot Smithing Process to Non-Ferrous Metals
14 Minute Read
The motivation for undertaking this research was to establish a more expedient process to achieve volumetric forms in non-ferreous metals. With the availability of commercial seamless tubings it seemed logical to develop working techniques adapted to this resource. I became involved in blacksmithing in 1971 and while developing the working technology of this area I began to realize that many of the processes of blacksmithing and silversmithing could be incorporated to work copper and copper alloys while in a heated state. This paper will deal with the application of shaping non-ferreous metals by forging and upsetting, by forming through sinking, dapping, stretching, raising and pressing, and by bending, twisting, cutting, punching, drifting, stamping, chasing, chiseling and rasping while at a red heat. Fabrication techniques of heated metal will also be discussed. There are no new discoveries in the process, but the research lies in the investigation. The numerous visual possibilities which occur are not possible to achieve without these applications.
METALS: COPPER AND COPPER ALLOYS
There are well over a hundred wrought products in copper and copper alloys available with each alloy varying in its physical working properties. I contacted the copper Development Association, Incorporated (405 Lexington Ave., N.Y., N.Y., 10017), and they sent a copy of Standards Handbook: Copper, Brass, Bronze; wrought mill products, Alloy Data/2. From this publication I was able to determine which alloys had the physical and fabricating properties for this process.
Copper No. 102 (oxygen free 99.95% pure) would be the ideal designate, but I have found to date that any copper designate with 99.3% or more copper content works excellent. High copper alloys (99.3% to 96% Cu) are also available and Alloy Nos. 192 and 194 have excellent working properties. These two alloys are used by the gift holloware industry. The prime considerations for the copper or high copper alloy used should be cost, availability, no lead content and its hot forgeability.
Rating should be 65 or higher as compared to Forging Brass No. 377 rating 100. For seamless tubing the local wholesale plumbing supply has available ¼" to 6″ diameter "DWV", "L", or "M" copper water pipe in 10′ or 20′ lengths which are excellent for forging and forming. Suppliers are listed in the bibliography and in C.D.A. Standards Handbook: Copper, Brass, Bronze; wrought mill products, Sources/5.
Brasses are copper alloys which have zinc as the principal alloying element. The wrought alloys comprise three main families of brass: copper-zinc; copper-lead-zinc (leaded brasses) ; and copper-zinc-tin (tin brasses). We find when we begin to select brasses, copper alloys with less than 96% copper are less versatile and more specifically used for one type of working process. For example, Cu Alloy No. 280 (muntz metal 60%) is excellent hot forming and forging (rated 90), but only fair for cold working. Cu Alloy No. 220 (commercial bronze 90%), No. 226 (jewelry bronze 87%), and No. 230 (red brass 85%) are excellent for cold forging and forming, but are rated only good for hot forming and not rated for hot forging. The best hot forging brass is Alloy No. 377 (rated 100). It is excellent for hot forming, but poor for any cold work with the exception of Mach - inability (rated 80) as compared to free-cutting brass No. 360 (rated 100). Also Cu Alloy Nos. 464, 465, 466 and 467 (naval brass) are excellent for hot forming and hot forging (rated 90), but only fair for being cold worked. First you need to determine the most advantageous process in making the object, then you choose the alloy best suited to the technique.
Bronzes are copper alloys which have tin as the principal alloying element. Today the term bronze is seldom used by itself in a technical sense. There are four main families of bronze alloys: copper-tin-phosphorus (phosphor bronzes); copper-tin-lead-phosphorus (leaded phosphor bronzes) ; copper-aluminum (aluminum bronzes); and coppersilicon (silicon bronzes). Excellent hot forming and forging Aluminum Bronzes are Alloy Nos. 624, 625 and 642, but these are only available in rod form. Silicon Bronze Alloy No. 651 (low silicon Bronze B) and No. 655 (high silicon Bronze A) are excellent for hot and cold forming, and good for hot forging. Cu Alloy No. 675 (manganese Bronze A) is excellent for hot forming and is rated 80 for hot forging.
With one exception Coppernickel alloys are not desirable for hot working. Alloy No. 725 is excellent for hot forming and cold forming, but not acceptable for hot forging.
In conclusion the available copper and copper alloys for the metalsmith is vast. It varies in type of stock (sheet, plate, rod, bar, wire, tubing, pipe and shapes) in dimensions, cross sections, and color (ranging from copper pink, gold brass, bronze reds, silicon white-gold, and nickel silver.) In our production as artists and technicians we have only touched upon the wealth of applications available when using copper and copper alloys.
HEATING SOURCES AND TEMPERATURES
If you build a small kiln with soft fire bricks to help hold the heat, heating with natural gas and compressed air or acetylene and oxygen is adequate for small work. But the real advantage to the process is in larger scale pieces. This requires a gas forge which can be simply made from one half of a 25 gallon metal drum lined with a high temperature castable refractory (maximum temperature 2300 degrees F), a small squirrel cage blower with electric rheostat control and propane (100 lb. tank supply) or natural gas (see diagram A). There are several fine commercial gas forges available such as the no. 122 or no. 133 from the Johnson Gas Appliance Company (see diagram B).
The use of coal or coke is limited because of the sulfur emitted when burning. I use a commercial coke containing less than one percent of sulfur for blacksmithing but this is not satisfactory for coppersmithing. The presence of sulfur and extreme heat causes a penetrating oxidation of the copper surface. The surface becomes very brittle and flakes off and the metal erodes at a very high rate. That which does not flake off remains as a brittle surface skin and may crack or separate when working of the metal takes place.
Charcoal is an excellent fuel when used in a blacksmith type forge (diagram C). It burns very clean with no traces of impurities, but its one drawback is the large volume of fuel you consume while heating the metal. Charcoal is inexpensive if you manufacture your own.
It is important to note that if iron has been used in the forge, the forge should be cleaned and new fuel be used for the heating of copper. Iron scale may contaminate the copper.
Depending on the specific alloy you're using, the working temperatures of the various copper and copper alloys range from 1250 degrees to 1650 degrees F (625 degrees to 900 degrees C). The working range is best described by the visual color of the metal at these temperature ranges. By my observation, a dull cherry red to a bright red-orange color of the heated metal describes the working range, but each person could interpret these colors differently. Therefore, establishing your own working parameters by experimenting at the outset is recommended.
There are four additional observations I've noted while working. The first observation is at the point when the metal is overheated. It literally drops off , not slumping or appearing to be melting on the surface. A few moments before this occurs the metal reaches a bright orange color and does not appear to change in color before melting. The second observation occurs while forging at a bright red heat. The metal becomes overly soft when hammered during a 30 degree to 50 degree F temperature decrease. This is noted especially when drawing a taper. This is also more apparent in larger diameter stock because of a slower drop in mass temperature through this range. The third observation is when forging copper you may continue to work through black heat and down until it's only a couple of hundred degrees in temperature or until the hammer blow leaves a shiney surface and begins to become resistant.
The fourth observation is most critical when you are forging the copper alloys (brasses and bronzes). Although I have not been able to test all the alloys noted earlier, those I have used verifies the following. If you forge the stock below its hot working temperature range it internally fractures even if the alloy is excellent for cold forging. Thus concluding, that like mild steel it becomes brittle at "black heat." It must pass through this temperature range and be at room temperature before working it cold. This does not appear to be the case when hot to cold forming of tubing. Generally, best results for hot bending or twisting copper and copper alloys are achieved at red heat. Bending and twisting above and below red heat are possible but extreme care must be taken to prevent edge cracking. Any cracks which develop are usually from forging not bending.
Tools are from the blacksmithing and silversmithing industry and are pre-World War ll. They have been modified and adapted as the need arises. The only limitations of a tool are imposed by the user.
WORKING TECHNIQUE
The techniques of hot forging and upsetting of rod stock are not unlike silversmithing, with the exception of the observations made earlier related to the heated metal itself. A variety of tongs and vise grips are used to securely hold the work. Extra metal should be allotted to allow for possible scarring from the tongs. The use of water to cool the adjacent metal as done while working hot steel is helpful because of the excellent heat conductivity of copper, Localizing the heat is the key to efficiency (photo D).
The hot forming techniques of sheet and tubing will be considered first. Again concentrating and localizing the heat to the specific area to be worked is necessary. This enables you to work the metal on itself. The metal which is not in red heat will be more resistant to shaping and that which is red hot is more plastic. Because of the circular cross-section of tubing, working around the circumference evenly by sinking or snarling results in uniform controlled forming. Obviously, any forming on supporting mandrels, stakes or dies is very desirable, but make sure no sharp metal edges are used. Great care must be taken with all hammers and surfaces of metal because the hot metal cuts very easily or can rupture from a knick in its surface while stretching.
Sheet may be formed rapidly by sinking or danping into a sand box, wood depressions in the end grain of a log section, or in laminated dies of composition board. Lead blocks, swaging blocks or any discarded metal forms (car bumpers) are varied and excellent for dies (photo E).
Stretching obviously takes place when dapping and sinking, but when using thicker gauge stock (14 ga. and thicker) controlled stretching or pressing is done. The resulting metal flow using these techniques at red heat results in an expedient process to achieve volumetric forms (photo F).
Care must be taken to maintain a uniform wall thickness. Traditional and altered stakes and anvils are used as supports. Power hammers like the "Little Giant" with a flat anvil plate and a ball peen drop head save a great deal of hand work (photo G].
Angle raising is less efficient but can be occasionally used. Handling has been the greatest drawback to dare. The best use is with tubing where you neck or splay the ends on a conical stake or mandral (photo H). Make sure the end of the tubing is filed smooth as any cut or notch will result in lateral cracking.
At a red heat bending and twisting usually can be accomplished in one heat. Make sure all the tools used are absent of sharp edges or serrated surfaces. A copper, lead or hard wood mallet is suggested when adjustments are needed. Cooling with water is again helpful to maintain or prevent bending and twisting to achieve uniformity.
The application of hot cutting, chiseling, piercing, and punching offers an immediate and direct process to the metal (photo I). The visual result of these techniques illustrates the hot plastic state of the metal. Stamping and chasing are also approached by the same application. The working temperature range is dull red to red-orange (1250 degrees to 1600 degrees F and 625 degrees to 900 degrees C). Although these techniques can be executed throughout this range, it is recommended to hot cut, punch, pierce and drift open thicker stock in the upper half of the temperature range (bright red to red-orange).
The ironsmith utilizes hot rasping to remove excess material and refine the piece before it cools below red heat. Copper and copper alloys may also be worked this way to expedite the process. The surface resulting from this technique offers various textural possibilities as well (photo J)
When executing these techniques it is suggested to wear gloves because the hand handling the tool is close to the work and valuable time is lost if the piece loses the proper heat before completing the operation. Longer stamps and chasing tools help avoid working too close to the hot metal. A saddle of mild steel to fit on the top plate of the anvil will protect it. This provides a surface which will not harm hot cuts and punches when penetrating through the stock. The final punching is done over a slightly larger hole than is being made (pritchell hole on the anvil is well suited). Constant cooling of the tool in water is needed so the temper is not drawn out while working the hot metal.
FABRICATION
The methods of hot fabrication have not yet been fully developed, but several possibilities are apparent. It is possible to chisel and chase to make channels for inlaying. In addition, the metal can be placed in a heated channel so that as the piece cools the contraction will secure the inlay. Hot riveting and collaring will tighten as the metal cools. Upsetting, crimping, or thickening the edges of nested tubing will contract as it cools thus providing a secure fit. Many other hot joining methods are possible with the shrinking concept. Variations of the open end mortise and tenon, interlocked and folded tabs offer possible hot joining techniques. Utilization of sheet metal crimpers, folders, stretchers and rollers offer additional interesting possibilities.
FINISHING
The finishing application ranges from the surfaces which are a result of the working process to the surfaces of traditional silversmithing. Wire brushing at dull red heat will provide a clean surface upon completion of the work. If the working oxidation is to be removed, the piece at this point is placed in a heated pickle solution. Wire brushing the oxidized surface patina, softly burnishing with a paste wax as a sealer and retaining the process marks as a final texture results in a direct statement (photo K). This is in contrast to a refined sanded and buffed reflective surface.
SAFETY
Normal safety procedures should be practiced with the addition of leather gloves, a heavy leather apron and above ankle work shoes with steel toes. High inpact safety glasses with side shields are a must. There is no need for tinted lenses unless working with oxygen and acetylene as a heat source. Ear plugs are usually overlooked, but should be used for prolong periods of hammering and while using any power hammering devices. A severe burn medication or a source for ice should be available. In the past, many blacksmith shops had broad leaf "aloe Ciliaris" succulents which contain a milk solution that could be applied to burns by breaking off a leaf.
BIBLIOGRAPHY
Information Sources
American Society for Metals, Metal Handbooks, Metals Park, Ohio.
Copper Development Association, Incorporated, 405 Lexington Avenue, New York, N.Y. 10017.
Copper and Brass Servicenter Association, General Office, 1900 Arch Street, Philadelphia, Pa. 19103.
Tool Suppliers
Buffalo Forge Company, P.O. Box 985, 465 Broadway, Buffalo, N.Y. 14203.
Centaur Forge, Ltd., 117 North Spring Street, Burlington, Wi., 53105.
Fisher and Norris, Incorporated, 301 Mohmouth Street, Trenton, N.J. 08609.
Johnson Gas Appliance Company, Cedar Rapids, la. 52405.
Suppliers for Copper and Copper Alloys
Alaskan Copper and Brass Company, 3223 Sixth Avenue South, Seattle, Washington 98134, 206/623-5800.
The Anaconda Company, Brass Division, 414 Meadow Street, Waterbury, Ct. 06720. 203/757-2021.
Bohn Aluminum and Brass Division, Gulf and Western Metals Forming Company, 23100 Providence Dr., Southfield, Mi. 48075. 313/354-4400.
Bridgeport Brass Company, Division of National Distillers and Chemical Corporation, 30 Grand Street, Bridgeport, Ct. 06602. 203/366-6182.
Chase Brass and Copper Company, Incorporated, 20600 Chagrin Boulevard, Cleveland, Oh. 44122. 216/283-3900.
Chicago Extruded Metals Company, 1821 South 54 th Avenue, Cicero, II. 60650. 312/242-2120.
E. Conklin Brass and Copper Company, Inc., 3244 West 23 rd Street, New York, N.Y. 10011.
Noranda Metal Industries, Inc., French Tube Division, P. O. Box 558, Prospect Drive, Newtown, Ct., 06470. 203/426-4431.
Phelps Dodge Brass Company, Tube Mill, 6100 South Garfield Ave., Los Angeles, Ca. 90022. 213/726-1000.
Precision Tube Company, Incorporated, Church Road and Wissahickon Avenue, North Wales, Pa. 19454. 215/699-5801.
Revere Copper and Brass Incorporated, 605 Third Avenue, New York, N.Y. 10016. 212/687-4111.
Uniform Tubes Inc., 200 West Seventh Avenue, Collegeville, Pa. 19426. 215/539-0700.
This project is supported by a grant from the National Endowment for the Arts in Washington, D.C.
Presented at the Society of North American Goldsmiths Conference in Seattle. These technical papers also appear in issues 13-16 of the Goldsmiths Journal.
by Thomas R. Markusen
You assume all responsibility and risk for the use of the safety resources available on or through this web page. The International Gem Society LLC does not assume any liability for the materials, information and opinions provided on, or available through, this web page. No advice or information provided by this website shall create any warranty. Reliance on such advice, information or the content of this web page is solely at your own risk, including without limitation any safety guidelines, resources or precautions, or any other information related to safety that may be available on or through this web page. The International Gem Society LLC disclaims any liability for injury, death or damages resulting from the use thereof.
Related Articles
Metals For Enameling
Waste Not, Want Not
A New Platinum Sterling Silver
White Metals and Alloys Testing
The All-In-One Jewelry Making Solution At Your Fingertips
When you join the Ganoksin community, you get the tools you need to take your work to the next level.
Trusted Jewelry Making Information & Techniques
Sign up to receive the latest articles, techniques, and inspirations with our free newsletter.